

The two lines are identical up until 5400rpm, where the standard sensor flat-lines while the 3 bar sensor goes on reading the true manifold pressure until 7600rpm. The second log is a 3 bar sensor that has been correctly re-scaled. The first log is with standard MAP sensor that flat-lines at 1.37 bar. The log file below shows two log files that have been added together in excel.
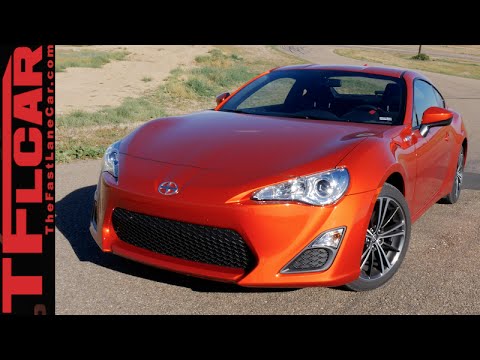
It generates a maximum output of about 260PS and a maximum torque of about. The next step is to fit new 3 or 4 bar MAP sensor and enter new scaling as above then repeating the test with the new MAP sensor to ensure it’s the same measured manifold pressure with the Ignition ON (engine not running) and at Idle. Bolt-on turbo system for 86 / BRZ, employing an actuator type metal flow turbine. The Preferred method to re-scaling the MAP sensor is to start with the standard MAP sensor installed and using Live Data, check the Manifold Absolute Pressure with Ignition ON (engine not running) and at stable Idle, you may want to make a quick log file to use as a reference. It is essential that the MAP sensor scaling is accurate for cranking fuel calculation and when using Speed Density Hell, run 16psi at redline with the stock injectors w/ stock turbo and the engine will probably blow up too. However run 22psi at 6500rpm with the stock injectors and the engine will blow up. I can run 22psi until 4000rpm and still only be at like 80 duty cylce. You can calculate the multiplier and offset for a sensor using the manufacturers data and some maths if required, however the popular plug-and-play replacement items are OMNI 3 and 4 bar sensors, the required offset and multiplier are shown below. The injectors don't max at any 'psi' level.
